Coating
Protecting Your Investment
A new tool can be expensive to buy. More so if it is custom made or modified for your application.
At Tru-Edge, we understand this from the very beginning with our engineering team working on your project. At that stage, we optimize design for manufacturing, which also includes in-house PVD coating capabilities from start to finish.
This allows us to develop our own solutions that match and exceed most specifications. It also enables us to maximize tool life and tool regrinding capability over time.
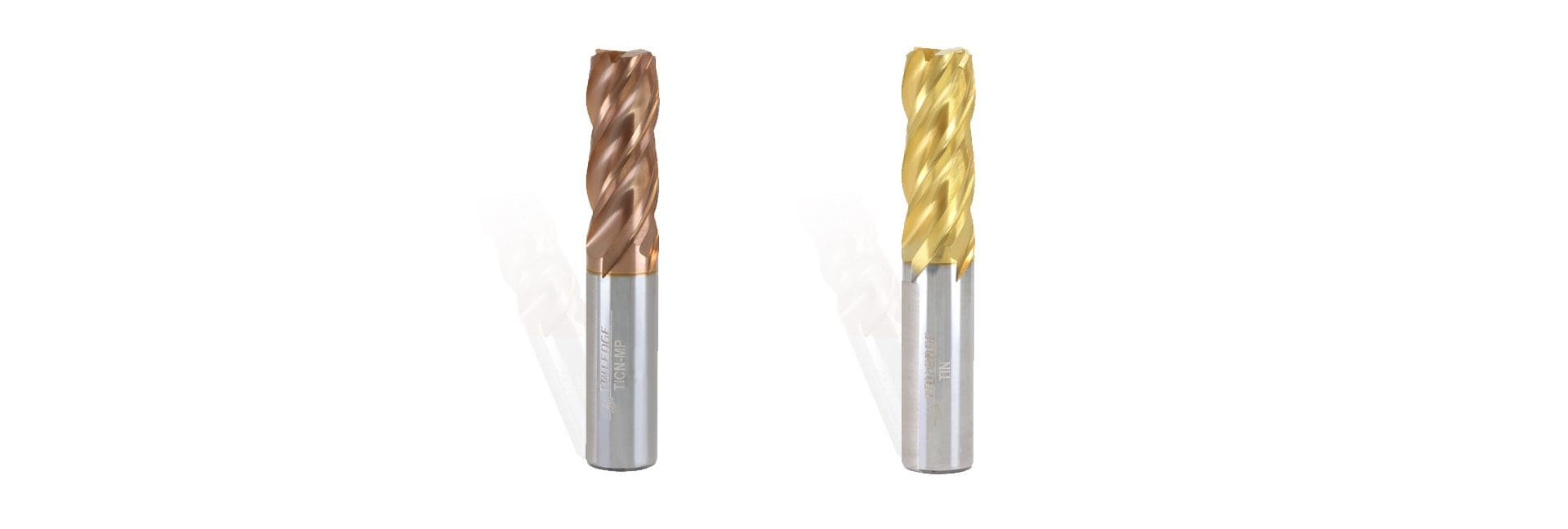
Tooling Component Coatings
FeinAl®
Superior PLATIT dependability in wear-protection and life extension for fineblanking operations.
Tru-PLEX™
A unique Tru-Edge solution with stoichiometry engineered for high production applications in the forming, punching, bending and deep drawing industries.
Tru-PLEX-CT™
Enhanced AlCrN based multilayer treatment with high wear resistance for forming and stamping applications.
CYBER-Coat MP™
A Tru-Edge enhanced TICN-MP coating for the stamping industry and traditional tool and die applications.
TiCN-MP
The Tru-Edge standard TICN coating for forming, stamping, and deep draw applications.
TiN
General-purpose treatment for injection molding and guide pins.
Cutting Tool Coatings
ALL4®
New generation QUAD Coatings4® to improve cutting performance in a variety of materials. This is the one to deploy to improve tool life over old generation AlTiN treatments- this is the Tru-Edge standard for universal applications.
TixCo4®
Fourth generation coating optimized for superhard machining and milling – great choice for hard-to-cut aerospace materials.
TixCo3®
Third generation coating optimized for drilling in wide range of materials, especially hard and abrasive metals. Good choice for dry or near dry drilling.
Tru-PLEX-CT™
Enhanced AlCrN based multilayer solution with high wear resistance against abrasive loads. Good heat and oxidation resistance. Performs well in milling applications. Outstanding for very dry applications.
nACo®
Nanocomposite solution with extremely high nanohardness and heat resistance – excels in high-performance, dry applications – think stainless steel milling.
nACrO
Nanocomposite solution delivering extremely high scratch and heat resistance. Exceptional for drilling steel and most drill applications.
TiCN-MP
Tough multipurpose treatment for interrupted cutting and milling.
ALTiN
Our old-generation coating used universally in cutting tool applications. For improved performance try the Tru-Edge ALL4®.
ZrN
Monolayer solution for reduction of edge buildup when machining aluminum (<12% Si content). With good resistance to heat, this solution is a great choice to machine titanium alloys.
TiN
General-purpose coating – the old standard. Unique application – apply the Tru-Edge “Flash Coat TiN” to indexable carbide inserts to enable operators to easily identify used and worn edges.
Color |
Hardness (HV) |
Thickness [µm] |
Friction (Fretting) Coefficient |
Max. usage temp. [ºC] |
|
ALL4® |
dark-grey |
3773 |
2 |
0.45 |
850 |
TixCo4® |
dark-grey |
4487 |
2 |
0.35 |
900 |
TixCo3® |
dark-grey |
4487 |
2 |
0.35 |
900 |
Tru-PLEX-CT™ |
blue-grey |
3600 |
2 |
0.5 |
900 |
nACo® |
blue-grey |
4181 |
2 |
0.4 |
1200 |
NaCrO |
light-grey |
4078 |
1 |
0.45 |
1100 |
TiCN-MP |
red-copper |
3875 |
2 |
0.25 |
400 |
ALTiN |
violet-black |
3263 |
2 |
0.6 |
900 |
ZrN |
white-gold |
2243 |
2 |
0.4 |
550 |
TiN
|
gold |
2651 |
2 |
0.4 |
600 |